Boosting PET recycling with higher standards for laboratory experiments
Researchers evaluated enzymes that break down plastic so that they can be put into industrial use more quickly
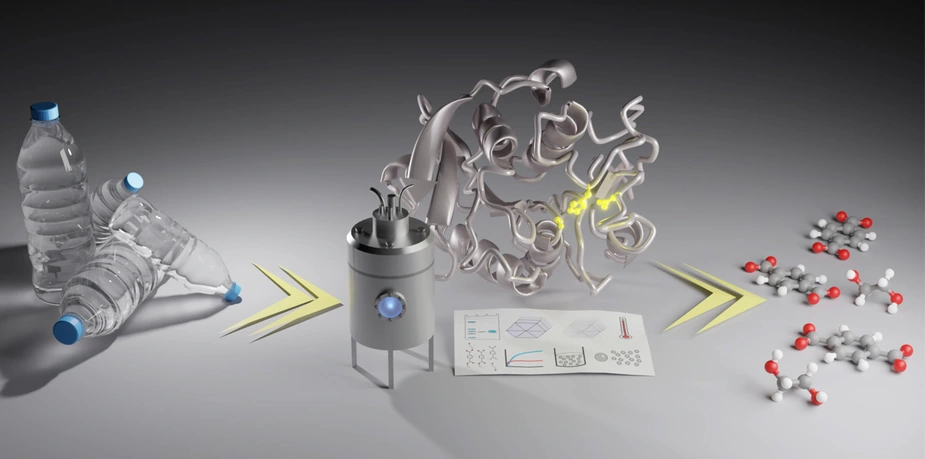
Many enzymes promise to break down plastic. But what works well in the lab often fails on a large scale. Now a new study by Gert Weber, HZB, Uwe Bornscheuer, University of Greifswald, and Alain Marty, Chief Scientific Officer of Carbios, shows how raising the bar for laboratory experiments could help identify promising approaches more quickly. The team demonstrated the new standards on four newly discovered enzymes.
PET recycling: lots of alleged breakthroughs
From time to time, media reports of major advances in the recycling of polyethylene terephthalate (PET). This is thanks to newly discovered enzymes, breaking down plastic into its constituent parts. However, the success story from the academic laboratory is usually followed by silence. PET accounts for 18% of the world’s plastic production, making it one of the most important plastics in terms of volume. Biotech company Carbios, for example, is building a plant in the north east of France by 2025. This plant will be able to recycle 50.000 tons of PET per year. They are interested to find the best possible enzymes for their industrial setup and have realised that many results from laboratory research cannot be transferred to a larger scale.
Upscaling experiments on PET recycling is difficult
“Some enzymes work great in laboratory experiments for a few hours, but they lose their activity very quickly and the substrate is not completely degraded,” says HZB expert Gert Weber. This is not a problem in the test tube in the laboratory, but it is when used in a large bioreactor. Together with the biotech company Carbios, Uwe Bornscheuer and Gert Weber show how new enzymes for PET degradation can be better compared with each other. “In order to allow upscaling later, many parameters must be within a narrow range even in laboratory experiments. The starting material must be precisely defined and the test protocols must be more standardised in order to better assess the performance of the enzymes and their application on an industrial scale,” explains Bornscheuer. The researchers have therefore developed a standardised PET hydrolysis protocol that defines reaction conditions relevant for hydrolysis on a larger scale. In particular, two PET materials were used, firstly a defined PET film and secondly PET granulate from waste bottles, as used by Carbios on a technical scale. They used these materials to test four recently discovered PET-decomposing enzymes: LCC-ICCG, FAST-PETase, HotPETase and PES-H1L92F/Q94Y.
When experimenting under this protocol, they found that two of these enzymes, FAST-PETase and HotPETase, were less suitable for large-scale use. This is mainly due to their relatively low depolymerisation rates. PES-H1L92F/Q94Y performed better. The fourth candidate, LCC-ICCG, outperformed the other enzymes by far: LCC-ICCG converts 98% of PET into the monomeric products terephthalic acid (TPA) and ethylene glycol (EG) in 24 hours. “In addition, we were able to reduce the amount of enzyme required for LCC-ICCG by a factor of 3 and the reaction temperature from 72 to 68 °C, which makes the use of this enzyme more economical,” says Bornscheuer.
Higher standards for experiments on PET recycling
“We should think about industrial applications already in our laboratory research,” says Gert Weber. After all, we are dealing with one of the really big problems of our time. Plastics are still being produced again and again from fossil raw materials, recycling rates are low and so far, it has mostly been a case of “downcycling” to inferior quality. Plastic waste can now be found in all bodies of water and soil and thus in the food chain. Progress is therefore urgent. “With these standards, we can do something to separate the wheat from the chaff more quickly.”
Original publication
ACS Catalysis (2023): Assessment of Four Engineered PET Degrading Enzymes Considering Large-Scale Industrial Applications
Grégory Arnal, Julien Anglade, Sabine Gavalda, Vincent Tournier, Nicolas Chabot, Uwe T. Bornscheuer, Gert Weber, and Alain Marty
DOI: 10.1021/acscatal.3c02922
Contact:
Helmholtz-Zentrum Berlin für Materialien und Energie
Dr. Gert Weber
Research Group Macromolecular Crystallography
gert.weber(at)helmholtz-berlin.de
+49 30 8062 14869
Dr. Antonia Rötger
Press Officer
Antonia.roetger(at)helmholtz-berlin.de
+49 30 8062 43733
Press release HZB, 24 November 2023