Nullkommanullnullnull-Toleranzen
Der schmale Grat zwischen Höchst- und Mindestmaß
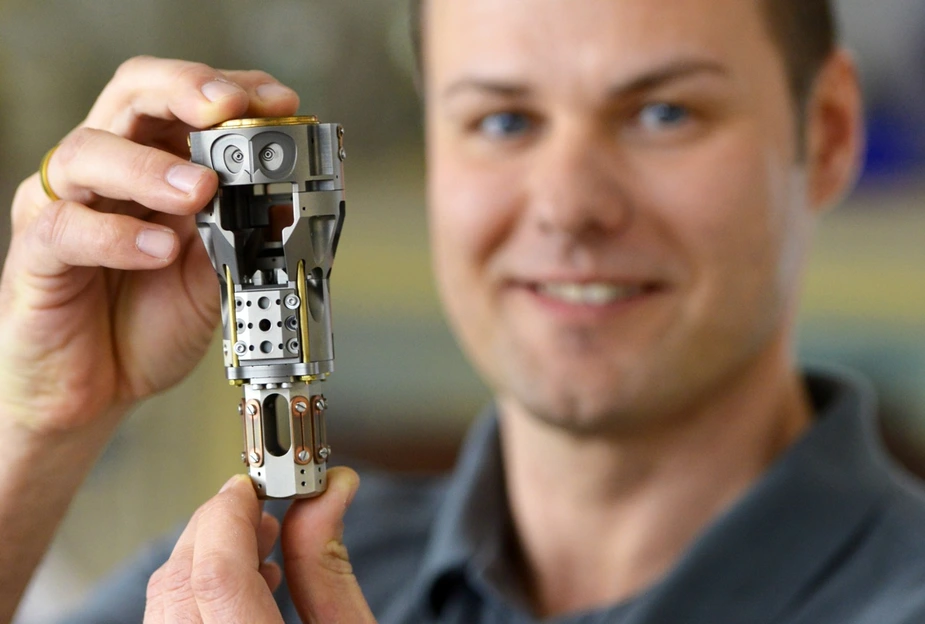
Brauchen Adlershofer Hightechfirmen und Forschungsinstitute Präzisionsbauteile, geht es zum Feinwerktechniker von nebenan. Für die Uwe Steingross Feinmechanik GmbH und die Astro- und Feinwerktechnik Adlershof GmbH bringt das immer wieder höchst komplizierte Aufträge mit sich.
Es brummt. Aus seiner Fertigungshalle voll 5-Achs-Fräsen und 8-Achs-Drehautomaten kommt Uwe Steingross ins kleine Büro – vertieft in ein Kundengespräch. Er nickt kurz und wendet sich noch beim Abschied vom Kunden zwei Mitarbeitern zu, die fachliche Fragen an ihn haben. Als der Firmenchef sich dann an runden Besprechungstisch setzt, ist er die Ruhe selbst. Obwohl der nächste Termin, bei dem es um die Bauplanungen für seine Firmenerweiterung gehen soll, schon bedenklich näher rückt.
Genauigkeit bis auf vier Stellen hinter dem Komma
Doch er ist sofort im Thema. „Toleranzen sind bei uns das A und O“, sagt er und wiegt eine hochkomplexe metallische Baugruppe in der Hand, die er eben im Vorbeigehen aus einer Glasvitrine gefischt hat. Sie gehört zu einem Rastersondenmikroskop, mit dem Forscher nanometergenaue Messungen durchführen. Im Vakuum bei Temperaturen nahe dem absoluten Nullpunkt fährt eine Spitze aus nur einem leitenden Atom darin im Raster über ebenfalls leitende Proben. Über Elektronenflüsse zwischen Spitze und Probe lassen sich Oberflächen nanometergenau vermessen. Was der Steingross in Händen hält, ist die Übersetzung zwischen Nanokosmos und grobmotorischem Anwender. Zwei Drehknöpfe erlauben es, die Proben über ein halbes Dutzend verwinkelter Zahnrädchen und Metallgelenke ganz langsam zu drehen und zu kippen. Im eingebauten Zustand liegt diese Mechanik im Vakuum, die Knöpfe außerhalb. „Bei der Fertigung solcher Highend-Bauteile erwarten unsere Kunden teils Genauigkeit bis auf vier Stellen hinter dem Komma“, erklärt er. Ein menschliches Haar wirkt in diesen Größenordnungen wie ein Baumstamm gegenüber Nähnadeln.
Neubau geplant
Mit seiner Steingross Feinmechanik arbeitet der Firmenlenker oft am Limit. Die Kunden kommen meist aus der Nachbarschaft. Hightech-Firmen und Forschungsinstitute, die hier Komponenten für Laser, Optische Geräte, für Medizin- und Biossystemtechnik oder für Vakuum und Weltraumtechnik fertigen lassen. Mit dem Wissenschaftspark wachsen die Aufgaben. „Wir arbeiten sieben Tage die Woche in drei Schichten und müssen dennoch 30 Prozent der Aufträge ablehnen“, berichtet Steingross. Der geplante Neubau soll das ändern.
Technische Limits
Während die räumliche Limitierung behebbar ist, gibt es technische Limits, die selbst für die erfahrenen Feinmechaniker unüberwindbar bleiben. Steingross greift im Regal hinter sich nach einer kleinen Pappschachtel. Darin winzige Edelstahlstifte, kaum halb so lang wie ein Streichholz. „Sie verbinden Herzschrittmacher mit dem Herzmuskel“, erklärt er. Bei genauerem Hinsehen zeigt sich, dass die Stifte außen fein gestuft und von innen hohl sind. Mit bloßem Auge ist schon die Bohrung kaum erkennbar. Doch in dem Auftrag ging es darum, dass sie von innen poliert und an eine innen liegende Kante zuverlässig entgratet sein sollte. Mit benachbarten Fraunhofer-Forschern hatten Steingross und sein Team ein Strömungsschleifverfahren soweit optimiert, dass sie die geforderte Innenpolitur umsetzen konnten. Doch letztlich hat er den Auftrag, bei dem es um eine zweistellige Millionensumme ging, doch abgelehnt. „Wir hätten 1.000 Teile die Woche liefern sollen, mit einer Fehlerquote von Nullkommanullnullnull“, berichtet er.
Verständlich, da die Grate im Innern die lebensrettende Funktion der Schrittmacher beeinträchtigten. Doch weil die Qualität im Inneren der Stifte weder mit optischen noch mit taktilen Messverfahren zu überprüfen war, sondern nur durch zerstörende Prüfung in Stichproben, waren Steingross die haftungsrechtlichen Risiken zu groß. „Es kommt sehr selten vor, dass wir an solche Grenzen stoßen“, sagt er. Doch die Vorarbeiten seien nicht umsonst gewesen. „Wir können jetzt einige Dinge, die wir vorher nicht konnten“, erklärt er, „etwa Löcher von nur 0,05 mm Durchmesser in hochfeste Metalle oder 0,3er-Löcher in Saphirlinsen“. Rein mechanisch versteht sich. Konkurrenz durch Laser fürchtet er nicht. „Die machen ja keine Löcher, sondern Krater“, so Steingross selbstbewusst. Das Telefon klingelt. Der nächste Termin. Schon einen Augenblick später ist er ins Telefonat über seine Baupläne vertieft.
Viel zu tun hat auch Michael Scheiding, Geschäftsführer der Astro- und Feinwerktechnik Adlershof GmbH. Maßhaltigkeit ist ihm ein Bedürfnis, doch er ist tolerant für das Chaos des Alltags. Beide Eigenschaften braucht er in seiner Firma, die etwa zur Hälfte mit Hochpräzisionstechnik für die Raumfahrt ausgelastet ist und daneben Spezialanfertigungen und Kleinserien für Kunden aus der Laser- und Halbleiterbranche sowie aus der Luftfahrt umsetzt. Das Gros kommt aus der Adlershofer Nachbarschaft. „Wir sind mit dem Standort gewachsen“, so Scheiding.
Know-how macht den Unterschied aus
Wenn nötig, fertigt Astrofein auf 5-Achs-CNC-Fräsen mit Fertigungsgenauigkeiten von fünf µm, also einem halben Hundertstelmillimeter. „Mit viel Erfahrung, genauer Kenntnis der Maschineneigenschaften sowie mehreren Arbeitsgängen mit zum Teil verschiedenen Aufspannungen des Bauteils ist das machbar“, erklärt Scheiding. Dieses Know-how mache den Unterschied aus zwischen üblichen Genauigkeiten von hundert bis dreihundert µm und den möglichen 5 µm. Bei der Einpassung von optischen Fasern, Linsen oder Spiegeln, die Laserlicht in maximaler Präzision auf Proben und Bauteile lenken müssen, kommen diese Differenzen Welten gleich.
Qualitätssicherung beginnt vor der Fertigung
Das Einhalten der Fertigungstoleranzen zu behaupten, genügt nicht. Kunden verlangen Dokumentationen und Messprotokolle. Die Qualitätssicherung beginnt bei Astrofein vor der eigentlichen Fertigung. Erst wenn genau vermessene Muster alle Anforderungen erfüllen, fängt der Serienprozess an, bei dem die Facharbeiter an den Fräsen sämtliche Parameter im Blick haben und wenn nötig nachjustieren. Abgenutzte Werkzeuge sind Tabu. Werkzeugmessvorrichtungen stellen sicher, dass die Maschinen beginnenden Verschleiß ausgleichen. Den Abschluss bilden automatisierte hochpräzise optisch-taktile Messungen im klimatisierten Messlabor.
Auch Scheidings Firma stößt hier und da an Grenzen – auch wenn viele ihrer Produkte im grenzenlosen Weltraum kreisen und teils eine zentrale Rolle beim Manövrieren von zig Millionen Euro teuren Satelliten spielen. „Wichtig ist, dass man seine Limits erkennt, bevor man einen Auftrag annimmt“, sagt er. Bei Astrofein gibt es keine Ultrapräzisionsmaschinen und gearbeitet wird auch nicht in klimatisierter Umgebung. „Unsere Maschinen kosten so viel wie ein Einfamilienhaus. Der Wert mancher Ultrapräzisionsmaschinen entspricht eher einem Schloss“, sagt er. Aktuell plane Astrofein nicht, in solche Anlagen und die dann nötige Highend-Mess- und Prüftechnik zu investieren. „Noch nicht. Eine Option für die Zukunft ist das aber durchaus“, verrät Scheiding. Genau wie der Technologiepark sei auch Astrofein noch lange nicht ausgewachsen.
Von Peter Trechow für Adlershof Journal
www.steingross.de
www.astrofein.com