High-strength printing
A PSC start-up team is producing high-purity silicon carbide with 3D printers
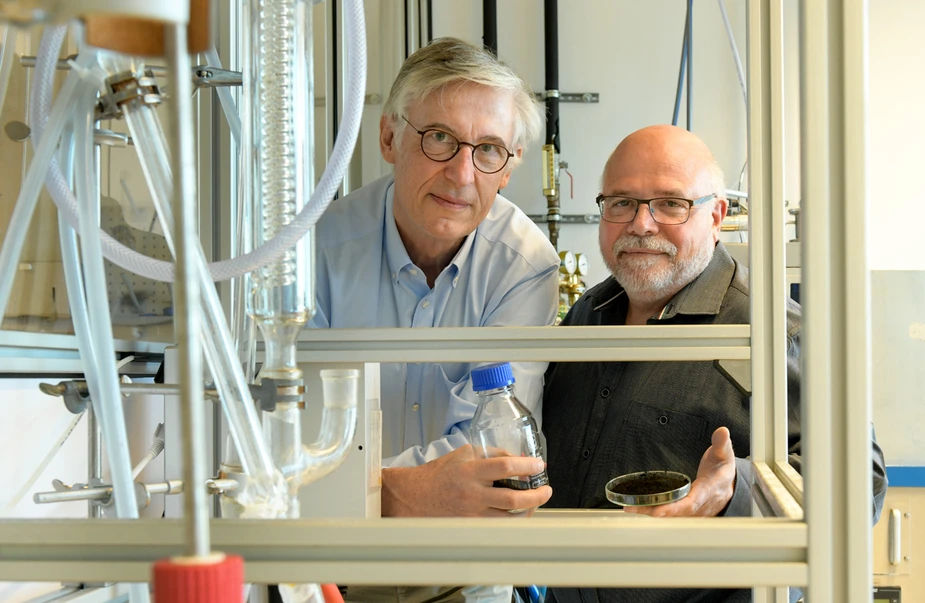
For a tenured professor to give up his position to start up a business, he must be extremely convinced of his idea. This is exactly what happened to Sigmund Greulich-Weber when he founded PSC Technologies GmbH in 2015. With his co-founder Ruggero Schleicher-Tappeser, he is working on printing self-developed silicon carbide alloys using a self-developed 3D printing procedure. If they are successful, this would enable the two business founders to tap into many different markets.
Silicon carbide is so hard that even diamond-equipped tools wear out quickly. It has high thermal conductivity and insulation, but low thermal expansion, and very low friction while being extremely corrosion resistant. During decades of research at the University of Paderborn, Professor Siegmund Greulich-Weber slowly unearthed the secrets of this semi-conductor material. One of the things he learned was that it is possible to alloy the crystalline structure of silicon carbide, thus gearing the already fantastic properties of this material towards specific applications. The method is also ideal for dealing with the material’s inherent brittleness. The alloys exhibit similar properties to high-strength steel. However, the crux of the matter remains: silicon carbide is too hard for abrasive tools like mills and drills. Moreover, the production process involves heating silica sand and carbon in ovens at over 200 degrees Celsius and uses vast amounts of energy. Lastly, the material must go through a laborious process to remove impurities.
Greulich-Weber left his university position and is now the full-time head of his own start-up, which he founded in 2015. The Adlershof-based company was co-founded by Ruggero Schleicher-Tapeser, a technology advisor, who assessed Greulich-Weber’s research in view of its potential for application in photovoltaics, and, as a trained physicist, quickly realised that he had discovered something special. Together they founded PSC Technologies GmbH; PSC stands for ‘pure silicon carbide.’
Why did they decide to give up secure jobs for the risks of entrepreneurship? ‘We are capable of producing high-purity silicon carbide from a self-developed precursor,’ says Greulich-Weber, pointing to a glass flask filled with black powder. The use of this powder makes the laborious cleaning process redundant and makes way for a novel production approach: the founders use selective laser beam melting to build silicon carbide components layer by layer. This procedure makes possible any conceivable design on a micrometre scale and facilitates cooling through built-in ducts. Combined with Greulich-Weber’s expertise in silicon carbide alloys, this has resulted in novel hybrid crystal metallic materials with an enormous market potential. The company is kicking off with milling heads, drills and other tools, but the 3D-printed high-tech material is also very promising for many other clean-tech applications, including high-performance electronics, battery or laser thermal management, and three-dimensional chips.
The Adlerhof-based start-up now already has six employees and an industrial-scale 3D printer at its disposal. ‘We decided that the metal powder bed system with two 200-watt lasers is oversized for our purposes,’ says Schleicher-Tappeser. Indeed, laser pulses with less than one watt are enough to stimulate a reaction in the precursor. The existing system will now be replaced with a multi-laser system with up to a million light sources that can write pixels at the same rate as a plastic printer. ‘This will enable us to achieve much faster build-up rate than all other metal printers on the market – and possibly also much cheaper because we use a precursor that is very cheap to produce,’ adds Greulich-Weber. This makes for excellent growth prospects.
By Peter Trechow for Adlershof Journal