Spooky materialisation where light beams meet
New processes from Adlershof-based xolo GmbH are revolutionising 3D printing
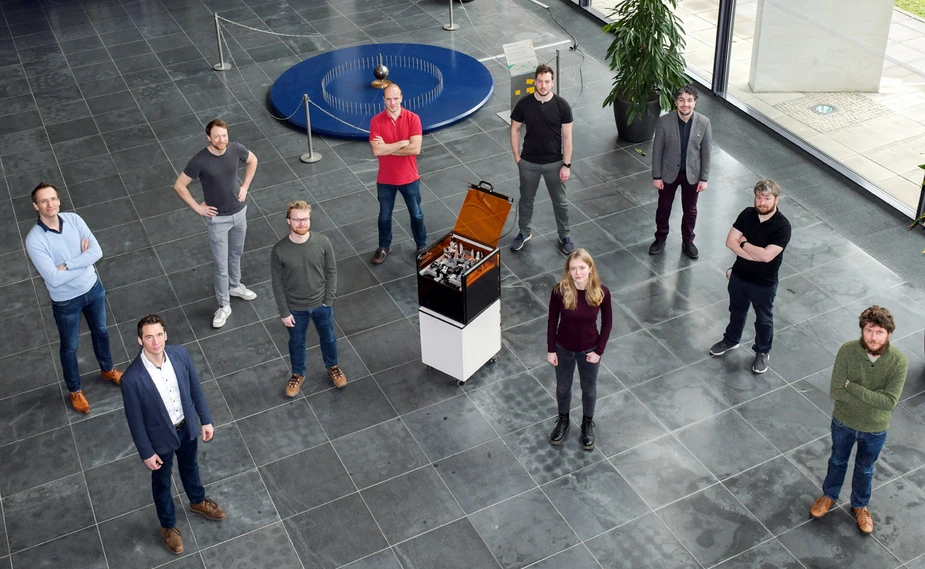
The young Adlershof-based xolo GmbH is launching a novel 3D printing process. Their xolography is based on molecules that are fused to form high-precision components under the influence of light beams of different wavelengths. The team is developing the hardware as well as the necessary materials.
From both sides of the glass printing space, a waver-thin wall of violet light divides the viscous mass that rests within it. It emerges from two diode lasers with a wavelength of 405 nanometres that excite specific molecules in the colourless resin – so-called photoswitchable photoinitiators (DCPIs). The violet curtain of light then turns into screen for a special presentation: Like in a time lapse, a projector casts thousands of sections of a component onto a continuously forward-moving wall of light. Behind it, the contours of the colourless mass are starting to show. After 5 minutes, the spooky presentation is over. Where the light waves of the projector intersected with the laser’s UV waves, the resin has been molded into a high-precision component. It is elastic at first. However, using UV light, it can be hardened in a way that makes it immune even to blows of a hammer.
This blazingly fast 3D printing process is called xolography. “Since the components are fixated by the viscous mass during the continuous, light-based construction process, they don’t require a supporting structure. Also, it makes the costly post-processing of other 3D printing procedures obsolete that are needed, for example, to smooth out layered surfaces or to remove supporting structures,” explains Martin Regehly, who developed the novel process with his schoolmate Stefan Hecht. Two well-known faces of Adlershof, who are now both professors in Aachen and Brandenburg, respectively, after succeeding in “Jugend forscht” young science competitions, starting their own companies, and completing PhD and habilitation theses. They grew up at the same pace as Adlershof over the past thirty years—and it is no accident that xolography found a home here in Volmerstrasse.
The now 10-strong team of xolo GmbH is headed by CEO Dirk Radzinski. He too is rooted in Adlershof, spearheaded the Humboldt Innovation GmbH, and supported many new businesses on the site. He has also been frequently involved in start-ups. “It is thanks to him and his extraordinary network that we could launch xolo with stable funding and an interdisciplinary team despite the pandemic-related restrictions,” says Hecht. Radzinski is in charge of operations, while the two natural scientists support the team in the background. Regehly contributes his know-how in solving optical challenges, Hecht his knowledge in organic chemistry as well as heaps of research experience in the field of functional materials. In addition to 3D printers, xolo is developing a broad range of suitable photoinitiators.
The scientists can think of dozens of ways to bring xolography to application. “Since the polymerisation of UV-curable molecules takes place in the micrometre range and we have achieved a highly homogenous material structure, the process is predestined for use in the manufacturing of optical components,” says Regehly. This could include free-form lenses, micro-optics, or miniaturised opto-mechanical systems. In biomedicine, it is suitable for manufacturing of microfluidic systems, pumps with integrated moving parts, or for printing tissue and implants. Hecht also envisions printing flexible grid structures that could serve as growth aids for regenerating cartilage in human joints.
First, however, the mission is to perfect the process and to develop new biocompatible and water-soluble DCPIs. The xolo team is aiming at increasing the already impressive build-up rates of 55 cubic millimetres per second using stronger lasers and projectors. The only spatial limitation, as far as Regehly can tell, is wideness, because the laser cannot project the waver-thin light curtain infinitely deep into the honeycombed material due to absorption. “However, it is indeed conceivable to print interminably by creating a continuous flow process, or to create 3D circuitry, multi-coloured components, or composite materials by targeted adding of material. With minds like theirs, Adlershof will surely have enough building material to stay a place creating future innovation for another 30 years.
By Peter Trechow for Adlershof Journal